Manufacturing plants are complex environments with many processes and systems that require careful planning and installation. One crucial aspect of setting up a manufacturing plant is installing platforms, which provide a stable foundation for equipment, workers, and materials.
When installing platforms in manufacturing plants, several factors need to be taken into consideration. These include safety, functionality, durability, and cost-effectiveness. This section will explore these factors to help you make informed decisions when selecting and installing platforms for your plant.
Table of Contents
The Safety of Workers and Equipment
The safety of workers and equipment is paramount when installing platforms in manufacturing plants. Ensuring a secure and stable platform significantly reduces the risk of accidents and injuries, which can have serious implications for personnel and productivity. The design and materials used in the platform must adhere to strict safety standards, including load-bearing capacities, slip-resistant surfaces, and guardrails where necessary.
Routine inspections and maintenance are vital to identifying and addressing wear and tear that could compromise safety over time. The team at www.erectastep.com places a strong emphasis on safety within its prefabricated platform solutions, offering customizable options that meet or exceed industry standards. By prioritizing safety, companies can create a safer working environment and reduce the risk of costly disruptions.
Functionality for Specific Processes
When installing platforms in manufacturing plants, it’s crucial to consider the specific processes they will support. Each platform should enhance operational efficiency, considering factors like height, layout, and accessibility for various tasks. For example, platforms should facilitate smooth material movement and easy equipment access, contributing to streamlined workflows.
The platform’s configuration should accommodate the manufacturing process’s unique machinery, tools, or storage needs. This involves assessing the frequency and type of tasks performed for assembly, maintenance, or storage. Customization may be required to ensure the platform adapts to changing production needs, minimizing downtime and boosting productivity.
Durability and Maintenance
Platforms in manufacturing plants are subject to heavy use and must withstand constant wear and tear. Therefore, choosing platforms made of durable materials that can withstand the demands of a busy industrial setting is essential. Steel is a common material used for platforms due to its strength, durability, and resistance to corrosion.
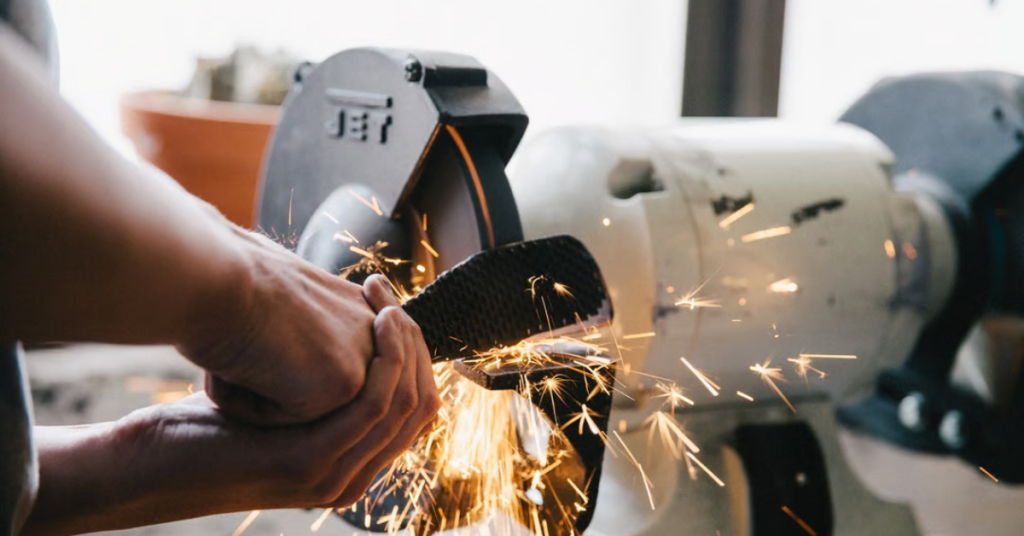
Regular maintenance is essential to keep platforms in optimal condition and prevent costly repairs or replacements. This includes cleaning, inspections, and promptly addressing any structural issues. Prefabricated solutions typically include manufacturer warranties and maintenance guidelines, making them a reliable option for companies seeking durable and low-maintenance choices.
Compliance with Regulations
Manufacturing plants must comply with regulations set by governing bodies to ensure the safety of workers and the environment. Platforms are also subject to these regulations and must meet requirements such as load capacities, dimensions, and materials. When choosing platforms for your manufacturing plant, it is essential to select those that meet all relevant regulatory guidelines.
In addition to government regulations, some industries have standards beyond basic safety requirements. For example, the food industry may require platforms made from certain materials or with additional features for hygiene purposes. It’s essential to research any industry-specific regulations that may apply when choosing platforms for a manufacturing plant.
Customization Options
When installing platforms in manufacturing plants, customization options are essential to meet each facility’s unique needs. Every manufacturing environment functions differently, with distinct workflows, equipment types, and layout configurations that can vary significantly. Choosing platforms with configurable features—like adjustable heights, modular designs, and custom sizes—can greatly boost operational efficiency.
Custom platforms can be designed to integrate smoothly with existing machinery and systems, making it easier to adapt to changes in production processes or equipment upgrades. Features like built-in storage solutions and specific access points can be tailored to optimize space and worker ergonomics. Choosing a manufacturer with strong customization capabilities allows businesses to create solutions that meet current needs and adapt to future changes, ensuring long-term functionality and effectiveness.
Cost-effectiveness
The cost of installing platforms in manufacturing plants can vary significantly depending on materials, customization, and maintenance requirements. It’s crucial to weigh the initial investment against the long-term benefits to determine the most cost-effective solution for your plant. While cheaper options may seem appealing, they may not offer the durability or customization needed for efficient operations. On the other hand, investing in high-quality, customizable platforms with built-in safety features and low-maintenance requirements can result in significant cost savings over time through increased productivity and reduced downtime.
Conclusion
Installing platforms in manufacturing plants is a pivotal aspect that can significantly influence operational efficiency and worker safety. Each platform plays a significant role within the broader framework of the manufacturing process, contributing to the stability and effectiveness of various systems. As such, businesses must take a thoughtful and strategic approach when selecting and implementing these structures. By prioritizing quality, compliance, and adaptability, manufacturers can create a robust environment that supports current needs and future growth.